バイオマスレジンHD・神谷雄仁CEO「ライスレジンで減プラ、日本の水田を守る選択肢の一つとなりたい」
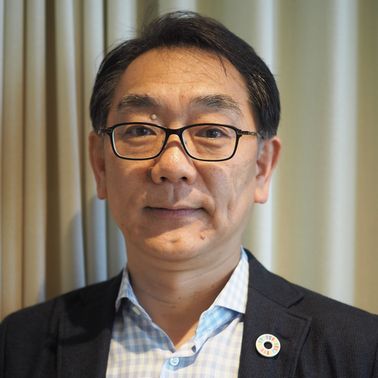
米を使用したバイオマスプラスチック「ライスレジン」。近年、食器など日用品への導入が進み、業界でもその存在感は高まりつつある。
それを手がける(株)バイオマスレジンホールディングスは、もともと2017年に(株)バイオマスレジン南魚沼として自社製造を開始、技術の向上と普及に努めてきた。米麦日報では、代表取締役・CEOの神谷雄仁氏にこれまでの経緯や展望を訊いた。〈インタビュー日=3月30日〉
――まずはバイオマスレジンHD設立の経緯を。
最初は米とバイオマスをめぐる流れを簡単にお話ししたほうがいいですね。国による最初の動きは、2002年に政府が立ち上げた「バイオマス・ニッポン総合戦略」だと認識しています。そこで最も推進されていた米の新用途はエタノール化でしたが、同時にプラスチック化も盛り込まれていました。当時のバイオマスプラスチック業界では木質系が比較的進んでいましたが、米でもこういった国の動きを背景に研究開発事業が始まったのが大まかな流れです。
当時、私は食品系の商社に勤め、農林水産省に出入りする機会があったので、そういった話は耳にしていました。ちょうどその頃(2005年)に開かれた「愛・地球博」で、アメリカの企業がトウモロコシを使用した生分解性プラスチックを紹介しているのを見ました。その時に「アメリカはトウモロコシだけど、日本は米だな」と感じましたし、既に米余りが起きていたため、米を素材として活用することが日本ならではの強みになるのではないかと考えていました。
また、商社時代は廃棄物となってしまう魚の頭や尻尾を油として再利用する仕事をしていたので、余りものには非常に敏感だったんです(笑)。「これはビジネスとして成り立つのでは」という嗅覚が働きましたね。ただ私は研究者でも科学者でもありませんし、ビジネスを構築することが専門でしたので、2007年にもともと米プラ化を研究していた会社と合弁で「(株)バイオマステクノロジー」を立ち上げました。
――そこからすぐ本格的な販売に向けて動き出したのですか。
当時はまだ“町の発明家が開発した米プラ”というレベルでしたので、世に送り出すことには苦労しました。現在の「ライスレジン」というブランド名はありませんし、製造拠点も持っていなかったため、委託生産を行っていました。様々なメーカーと協業を続けたなか、2010年に発売されたピープル社の「お米のおもちゃシリーズ」は比較的早い段階で製品化され、現在も高い支持を得ています。
とはいえ、当時の技術には課題が多く、レジ袋に採用すると手触りがざらついていたり粒感が残っていたりと、今ほど汎用性の高いものではありませんでした。やはり自前で技術を深掘りしなければ、プラスチックの代替にはなり得ない――そんな想いから2017年、南魚沼に「(株)バイオマスレジン南魚沼」を立ち上げ、自社工場を建設して本格的な研究開発・生産を開始しました。
――「ライスレジン」というネーミングに変えたのもそのタイミングですか。
そうです。それまでも別の名前で商標権を取得していたのですが、ブランディングの意味も込めて新しく考えることになりました。「米を使っているから『ライスレジン』なんて良いんじゃないか」という軽い気持ちで申請したら、上手い具合に商標が取れてしまって(笑)。ロゴも制作して、工場の用地は米産地にこだわって探しました。バイオマステクノロジー時代は試行錯誤を重ねた10年間でしたが、2017年に「ライスレジン」として南魚沼で再スタートを切るという気持ちでしたね。
――ライスレジンの製造技術とは。
本来は混ざりにくい米と石油を混ぜながら一つの物質に仕上げる、技術用語では“混練”という製法を採っています。プラスチックも米も熱を加えれば柔らかくなり、冷めれば硬くなるという性質は同じですので、米をアルファ化し、糊のような澱粉状に加工して混ぜるという形です。原料は非主食用米(米プラ専用米)として作付したもの、酒米搗精時に発生する米粉、特定米穀、食用不適米穀にあたるような古い年産の米など多岐にわたります。
――設立当初から技術もかなり進歩したかと思います。そのカギとなるものは。
混ぜ方や反応の起こし方など技術面での進歩もありますが、最も重要だったのは原料米の管理ですね。
ご存じのように銘柄によってアミロース含量や食味は異なりますが、特性を細かく管理して銘柄や粒の形状などを均一に揃えると、仕上がりの品質に安定感が出てきます。やはり3等のブレンド米よりは1等の単一銘柄の方が扱いやすいですし、数年前までは「どんな米でも出来ますよ!」なんてことを言っていましたが、最近は「お米はちょっと選ばせてくださいよ」とお願いするようになりました。
品質の均一化が大事と申し上げましたが、そもそも米は流通上の管理がしっかりしているので、当社が手掛けるバイオマスプラスチックのなかでも非常に使いやすい原料だと感じています。温度管理をはじめ、年産や銘柄などのトレーサビリティもありますし、それらの情報がプラスチックの特性にも表れます。そのデータを蓄積することで「この地域のこの銘柄ならこんな特性になるのでは」という新たな引き出しも増やしてきました。
また当社は、南魚沼に加えて福島と熊本にも工場を構え、工場ごとに集まる米も異なります。拠点が増えると別の気づきも生まれてくるので、またそれを蓄積して、例えばベトナム工場では長粒種からプラスチックを製造するなど、技術の発展に活かしています。通常のプラスチック業界は品質の安定が命なので原料のバラつきはないのが当たり前ですが、我々の相手は植物です。多少ブレることを前提に、如何にして安定した品質を提供するか――この点に関しては合理的な判断と技術の蓄積を重ねた結果、今日の姿があるのだと思います。
――現在はどのような製品展開を。
バイオマスプラスチックもPE(ポリエチレン)やPP(ポリプロピレン)など配合するプラスチックによって性質や強度が変わりますので、現在は3種類のマスターバッチを展開し、さらに取引先のニーズに合わせて配合を変える方式を採っています。例えばお米の歯ブラシにはライスレジンを30%、近々発売するランドセルには10%――といった具合です。
我々が一次産業として原料を供給し、各メーカーの技術によって最終製品へと加工されますが、先ほど申し上げた通り、米によって製品の出来が左右されることが分かってきました。今後はマスターバッチを15種類程度に細分化し、より使いやすいものを提案したいと考えています。
――減プラ全体で見ると、近年の米業界では石灰石を使用した「LIMEX」の米袋が登場しています。様々な代替素材があるなかで、ライスレジンの優位性とは。
それぞれ役割があると思いますし、もちろん、ライスレジンも万能ではありません。先に弱点をお伝えすると、米を使用している以上は完全な透明にならない点です。例えばイチゴ用の包装フィルムなど、色を鮮明に見せたいものには不向きかもしれません。供給能力的にも全てのプラスチックの代替とはなり得ませんし、それぞれの長所を活かして上手く棲み分けができれば良いですね。
ただ、植物由来である点と強度を総合的に見ると、ライスレジンの強みは使い勝手が良いことですので、日常の大部分の使い捨て用品には参入できると思います。逆に半導体や自動車の部品など精密機械関連には難しいと感じていたのですが、最近はEUの自動車メーカーからの問い合わせが非常に増えています。
EUでは各国に先んじて大規模なプラスチック規制が進展しつつあり、メーカーとしては減プラが必須事項なのです。こうした動きは今後も増えると思いますし、我々もニーズに応えられるよう、技術をブラッシュアップしていきます。
一方、米袋のような産業資材は要求レベルが高く、こちらも更なる技術開発が必要ですね。ライスレジンと米関連製品は親和性が高いため、包材ではテーブルマーク(株)のパックご飯の外装フィルムに採用していただきましたし、近い将来、パックご飯のトレーやおにぎりのフィルムなどにも使われる時代が来るのではないかと期待しています。とはいえ要求レベルは高いので……温かい目で見守っていただければ幸いです(笑)。
――品質のカギを握る原料米の調達は。
南魚沼・福島・熊本の各拠点で調達を行っており、生産者との契約栽培で全量買取という形と、卸から特米や米粉を調達する形の2つが主な調達方法です。原料米の本格生産は2019年から開始し、東川町農協(北海道上川)や(株)モスファーム熊本(熊本県八代市)など、全国に広がりつつあります。品質の均一化は求められますが食味は考慮しなくても良いので、生産者の方々と一緒に効率重視の生産を目指し、農研機構九州農研と連携した再生二期作栽培や農工大監修の超多収品種「さくら福姫(モンスターライス4号)」に取り組んでいます。
現在は主食用米の消費減少により、代表的なブランド産地ですら苦労している時代です。この事業を始めた頃は「米がプラスチックなんてけしからん!」なんて意見をいただいたこともありましたが、今は生産者の皆さんから意義を理解・共感してもらっています。
企業も同様で、モスバーガーとの取り組みのように遊休地を活用して米を生産し、ライスレジンに変えるという試みは、持続可能性が叫ばれる現代社会においてとても分かりやすいものだと思います。
また特米の調達でいうと、(株)バイオマスレジン関西は幸福米穀(株)との共同会社になるため、卸としての機能も持ち合わせています。それぞれの子会社が地域の特米卸とお付き合いしており、最近では真っ先にお声がけいただくこともあります。逆に我々からも特米卸に品質管理をお願いしていますので、しっかりとした関係性が築けているのではないでしょうか。
――米価が上がっている令和4年産ですが、原料米のコスト管理は。
我々もメーカーに供給する立場である以上、原料米は1円でも安いことが望ましいので、それを踏まえた調達・コスト管理を行っています。価格の目安は飼料用米と同水準とし、契約栽培分は新市場開拓用米として補助金を活用しています。ただ、やはり飼料用米よりも交付金単価が低いため、生産者にご苦労いただいている面もあると思っています。そうしたお互いのジレンマ解消のためにも、「できるだけ生産コストを下げながら単収を上げましょう」「一緒に生産性を上げていきましょう」と呼び掛け、協力し合っています。
もちろん、ライスレジンとなる米だけを生産して主食用米のような農家所得が実現できるわけではありません。米の需給や今後求められる多角的な農業経営を考えると、ライスレジン用米が作付の選択肢の一つとして認識されることを望んでいます。
――主に海外向けで、米由来の生分解性プラスチック「ネオリザ」の展開を始めていますね。
実は、バイオマスプラスチックの普及はアジア諸国のほうが進んでいるのが現状です。特に途上国では街中にゴミが野積み山積みになるなど、ゴミの処理問題が深刻化しており、生分解性プラスチックの導入が急務の状況です。微生物によって水とCO2に分解できるネオリザならばそうした問題の解決に貢献できますし、米のみならずキャッサバやデーツ(ナツメヤシ)などの残渣との組み合わせも可能ですので、本来は廃棄されてしまうものの新たな活用方法として提案しています。
また、国内でも肥料被膜材にネオリザを活用する取り組みが始まっています。近年、主に一発肥料の被覆殻が河川や海洋に流出するマイクロプラスチックとして問題になっています。その代替としてネオリザの有効性に着目いただき、今春から三洋化成工業(株)と実証を開始します。既に多くの問い合わせがある状況です。
――今後の展開は。
まずは国内の製造拠点を10か所に拡大することが目標です。仮に、北海道で巨大な工場を建設して九州に輸送すれば輸送コストが嵩むので、現実的ではありません。工場を全国各地に点在させ、連携を取りながらバランスの取れた供給体制を構築していきます。
また、拠点を増やすにあたって、行政との連携は前提条件と考えていますので、今年2月に新潟市と締結した連携協定をモデルに拡大していきたいです。「みどりの食料システム戦略」に伴って各都道府県が基本計画を策定しましたし、自治体にも環境負荷低減の推進が求められてきます。我々と連携することで、マイクロプラスチックの削減や中干し期間延長によるメタンガス排出抑制など、ゼロカーボンシティに向けた各自治体の取り組みを後押ししていければと思います。
現在、国はバイオマスプラスチックの導入目標を2030年に約200万tと掲げています。そこで当社も5%程度のシェアにあたる10万tを目指します。米の配合が50%ならば米の使用量は5万tですので、ある程度の規模感に達することができるのではないでしょうか。ただ、現在は3工場の生産能力をフルに使って1万t程度ですから、なかなかハードルは高いですね。同時にアジア全域に向けて技術のグローバル化を図ること、事業拡大に向けた株式上場も見据えていければと思います。
また、ライスレジンやネオリザの拡大・普及は減プラだけでなく、水田機能の維持にも繋がります。例えば、近年は大雨による災害が激甚化するなか、水田のダム機能が再評価されています。遊休地・休耕田を活用する当社の取り組みはこの点に寄与できます。また、我々の手掛ける米は食味が劣っていても有事には食用となり得ます。
食料安保の機運が高まる今、改めて水田の意義が評価されていますし、生産者には水田を守る選択肢の一つにプラスチックがあるということを知っていただきたいです。我々はプラスチックメーカーですが、日本の米作り、そして日本農業を維持・拡大していきたいという想いで、今後も事業を展開して参ります。
――ありがとうございました。
〈米麦日報2023年4月13日付〉