【大手みそメーカー生産管理者に聞く】生産計画は1人50~100品担当/マルコメ
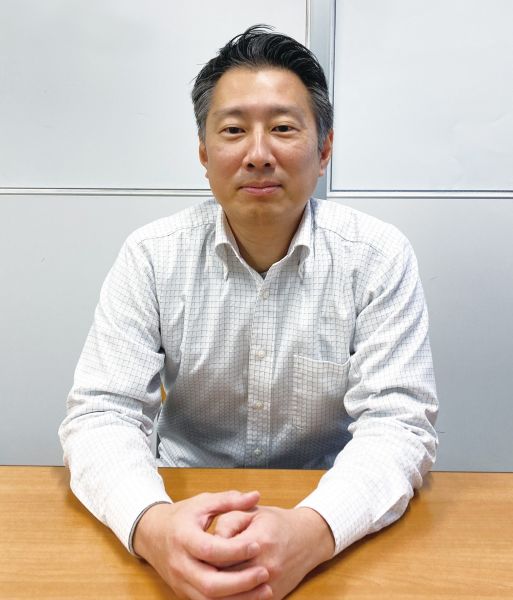
〈みそは仕込み原料から遡り数カ月前から仕込みの計画を立てる〉
マルコメは多種多様な製品群を持っている。当たり前のように自社の商品が店頭に並ぶのは、いわば黒子の部隊の働きが重要になってくる。需要予測をして、生産、配送までを管理する生産本部生産サポート部の鈴木一朗部長に話を聞いた。また、今回は生産することで排出される廃棄物の処理を担当する環境課の中村昌貴課長にも話を聞いた。
──生産本部生産サポート部の仕事内容について
鈴木部長 生産計画ではどの商品をいつ、どれだけ作るのかを生産部門に指示する。数百アイテムに及ぶため、限られた人数の中で1人50~100品くらいを担当する。出荷や売上実績などを加味しながら予定を組むため、各担当が生産部門と生産ラインの状況や人員も含めて打ち合わせしながら計画を決めている。月によってばらつきがある商品は、次月以降の生産をどうするかが大切で、欠品もできない、作りすぎて滞留もできないため、在庫がしっかりと回るような形で生産計画を組むことが一番難しいところといえる。
──毎日の作業内容について
鈴木部長 みそ、即席みそ汁、「大豆のお肉」、糀関連の管理出荷実績と今後の見込みを考えながら計画を立てる。みそは仕込みの原料から遡って行うため数カ月前から仕込みの計画を立てなければならない。みそには、調味みそもあるため、みそとは別に、どのくらい仕込むか考える。これから新製品の時期になるので、前年数字のない新製品を、どのくらい作るか、見込部分は開発部門やマーケティング部門と連携しながら、欠品しないように準備しなければならない。また、各部門で部会を定期的に行っているが、各部門で課題や取り組みを共有して、品質ロスがないように日々取り組んでいる。
──物流における課題への取組について
鈴木部長 トラックの確保が難しくなってきている。そのため、物流会社の課題や問題点も一緒に解決していく必要も出てきた。オーダーのリードタイムを1日伸ばす、バラで積んだものを減らす、正パレットや面単位にして倉庫で働く人の負担を減らすなどの取り組みを行っている。また、納品時の待機時間に関する問題は予約システムで解消するところが増えている。24年度からトラックドライバーの時間外労働の年間上限は960時間と定められた。今後、トラックがあっても運べないところがでてくる可能性がある。物流各社は年末年始、夏季休暇をきっちりとるようにするなど、無理な配送をしないようにしているようだ。
〈廃棄物を約40種類に分別、焼却可能な物は火力発電の助燃材に〉
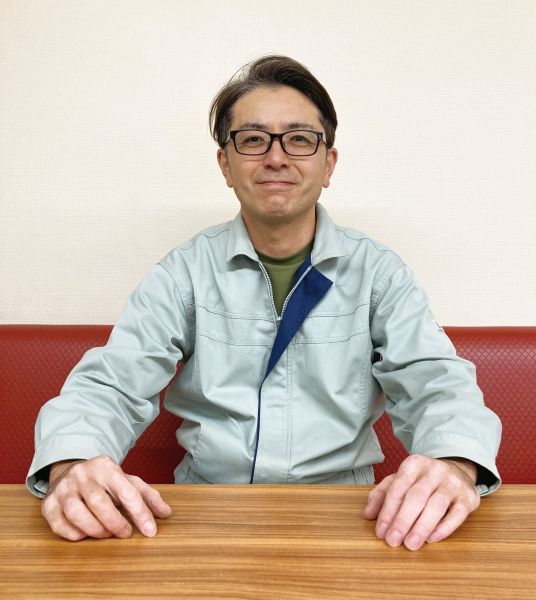
──環境課の担当作業内容について
中村課長 工場で使用している水や生産から出てくる排水処理、廃棄物関係を担当している。電気、ボイラーなどの運転管理、省エネ、CO2削減に取り組んでいる。工場では、廃棄物を約40種類に分別して排出している。各現場から分別されてきた廃棄物を、プラスチックであればチップ原料や、焼却できるような物は火力発電の助燃材として排出する。紙は再生使用できるため、再生原料として排出する。食品系の残渣物は飼料としての利用や、堆肥にして農地に戻して野菜を作るようなことも行っている。現在、産業廃棄物を有効活用する手段として、リサイクル化する品目も増えてきた。工場で廃棄されている廃棄物の8割ほどをリサイクル化している。リサイクル化では、排出者がいかに細かく分別するかが重要になってくる。ここでゴミになるのか、資源になるのかが決まるためだ。
段ボールは紙の資源になり、収益になるものもある。コピー用紙は上質紙になる。紙としてまとめるのではなく、細かく種類分けした上で紙資源として買い取ってもらう。原料として米、大豆の選別から落ちたものについても飼料としては価値がある。製造工程でロットアウトしてしまった大豆ミートは栄養価が高く、飼料化に適している。このような取り組みによって産業廃棄物の処分費が発生せず、生産活動の中では廃棄物費用の低減、圧縮につながっている。常に工場からの出口を見て、リサイクルできるものがあれば、それを工場側にリターンして分別してもらう。そこでは、受け入れてくれる取引業者の選定が大事になってくる。
新商品が出ると今まで出ていたゴミとは違うものが発生するため、リサイクルできるものがないか。多く発生しているものの中で、きれいなプラスチックを有効活用してくれるところはないか。日々その辺りの情報は産廃業者やリサイクル業者から情報をもらいながら取り組んでいる。工場から出る廃棄になるものを焼却するとCO2が発生、環境汚染につながるため、できるだけそういったものを減らすところから取り組んでいる。工場で使用する電気消費量の削減も行っている。蒸気が漏れている可能性があるところやコンプレッサーの漏れを一つ一つパトロールをする中で、早く修繕してロスを無くす。それは省エネにもつながっている。
工場で使用している資源、電気、ガス、水道など、全てにメスを入れていく必要がある。工場で使う水の量を少なくする。電気もガスも。通常通りの生産には無駄が隠れている。この無駄をいかに分かるような形にするかが課題。いま取り組み始めている電気は、電気を配る動力盤に電気使用量の計測器を付けた。一つ一つの機械が、どれだけの電気を使用しているかを見えるようにして、細かく突き詰めていくことで、見えづらかった無駄を省くことが可能になった。
〈大豆油糧日報 1月23日付〉